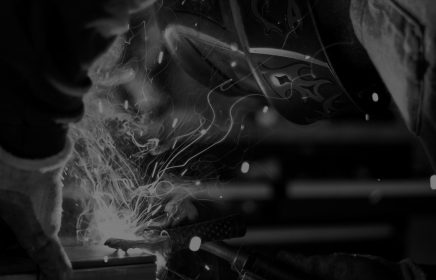
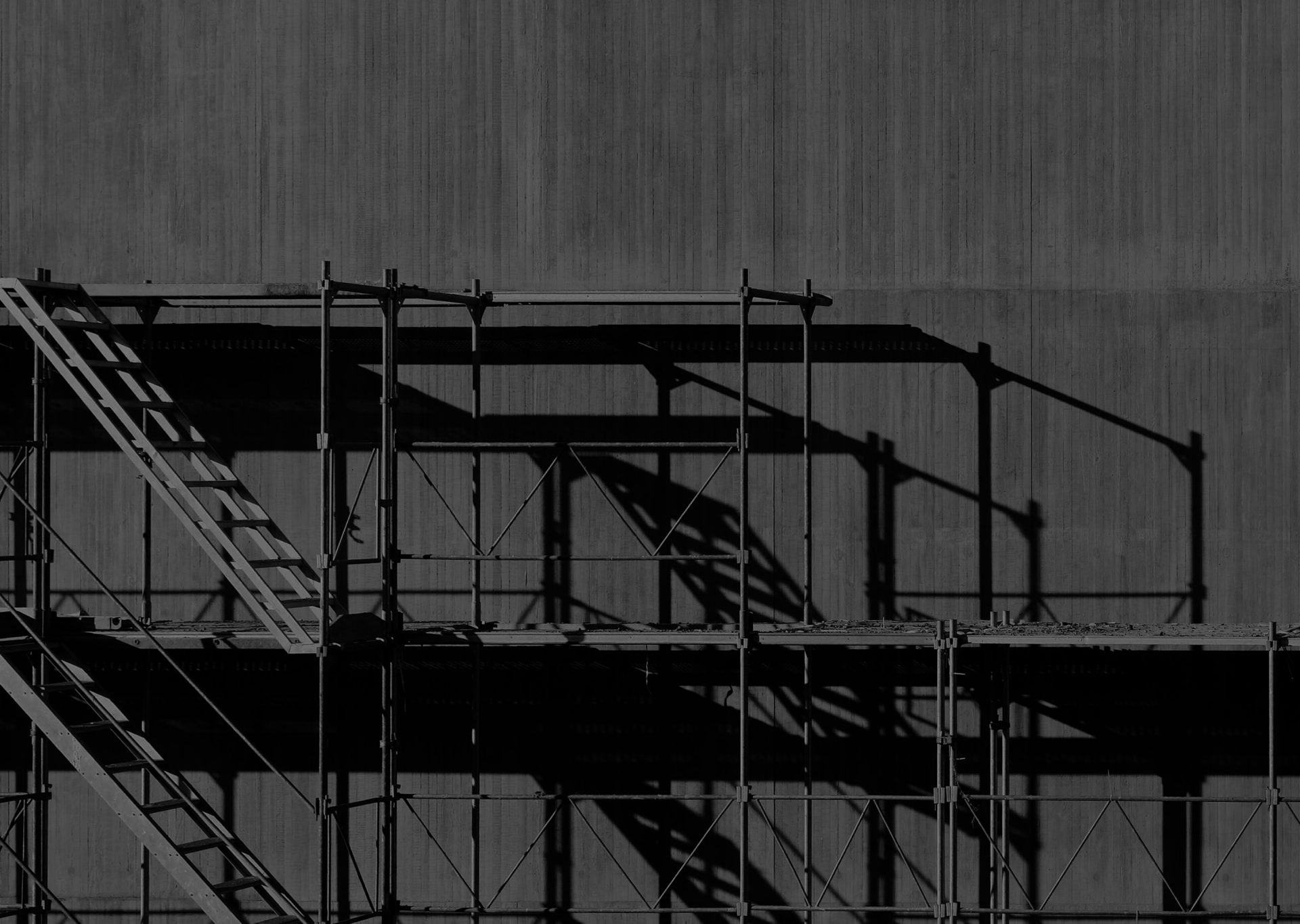
Digital Construction Tech
Technologies Transforming Construction
Technologies Transforming Construction.
There are six major technologies involved in digital construction that individually and collectively offer the big benefits to clients of lower costs, lower risks, fewer delays, less disruption during construction and higher long-term asset values with lower running costs. Some… Read More
Technologies Transforming Construction.
There are six major technologies involved in digital construction that individually and collectively offer the big benefits to clients of lower costs, lower risks, fewer delays, less disruption during construction and higher long-term asset values with lower running costs. Some of these technologies have been around for a decade or more, and are mature and ready to use.
Before we look at the challenges of getting the most from the technology, it is worth briefly explaining each technology.
There are six major technologies involved in digital construction that individually and collectively offer the big benefits to clients of lower costs, lower risks, fewer delays, less disruption during construction and higher long-term asset values with lower running costs. Some of these technologies have been around for a decade or more, and are mature and ready to use.
Before we look at the challenges of getting the most from the technology, it is worth briefly explaining each technology.
Digital surveying, geolocation and drones
Digital surveying, geolocation and drones
Construction needs to happen in a landscape, so one of the first requirements of a project is to collect data on the landscape to help decide the master plan.
This has gotten much quicker and easier with digital. There is a large amount of data, digitally available, often from public sources. Maps, photos, 3D models of sites and cities and copious amounts of data on geology, flood risks, demographics and economics are freely available if you know where to look and how to pull it together.
This takes time and cost out of the front-end analysis, but also allows for better decision making, more options to be explored and decisions to be made with more certainty. It also allows designs to be brought to life. A digital model of the future construction, located in a digital model of the landscape, allows you to see what it will really look like when you look out of the window.
Satellite data or city scans captured from aircraft is typically only accurate down to 15cm-50cm. That is fine for master planning and concepts stages but often not good enough for detailed design. Coverage varies widely as well; major, modern cities are often very well covered with existing data; remote countryside much less so.
Capturing survey data from the field is changing fast. There is still a place for the traditional approach using tripods to measure accurately by hand in 2D, but a much richer source of data can be captured using 3D photogrammetry, drones and laser scanning. Laser scanning can capture very fine details, down to the millimetre level, which is very useful if you are changing a building or existing infrastructure, as you can get a fully detailed and accurate model of the existing reality to design from. The cameras can be handheld (for scanning interiors) or on drones (to scan the outside of a building or a site). Photogrammetry can achieve 1-3cm accuracy which can be equivalent to standard laser scanners.
New digital surveying technology doesn’t just help with the design. When managing a large project on-site, it is very hard to see what is going on to track progress and to get a “helicopter view” of the project. Photographs from drones, can be processed using photogrammetry techniques and combined with laser scans to produce a “digital twin” or 3D model of a site.
Construction needs to happen in a landscape, so one of the first requirements of a project is to collect data on the landscape to help decide the master plan.
This has gotten much quicker and easier with digital. There is a large amount of data, digitally available, often from public sources. Maps, photos, 3D models of sites and cities and copious amounts of data on geology, flood risks, demographics and economics are freely available if you know where to look and how to pull it together.
This takes time and cost out of the front-end analysis, but also allows for better decision making, more options to be explored and decisions to be made with more certainty. It also allows designs to be brought to life. A digital model of the future construction, located in a digital model of the landscape, allows you to see what it will really look like when you look out of the window.
Satellite data or city scans captured from aircraft is typically only accurate down to 15cm-50cm. That is fine for master planning and concepts stages but often not good enough for detailed design. Coverage varies widely as well; major, modern cities are often very well covered with existing data; remote countryside much less so.
Capturing survey data from the field is changing fast. There is still a place for the traditional approach using tripods to measure accurately by hand in 2D, but a much richer source of data can be captured using 3D photogrammetry, drones and laser scanning. Laser scanning can capture very fine details, down to the millimetre level, which is very useful if you are changing a building or existing infrastructure, as you can get a fully detailed and accurate model of the existing reality to design from. The cameras can be handheld (for scanning interiors) or on drones (to scan the outside of a building or a site). Photogrammetry can achieve 1-3cm accuracy which can be equivalent to standard laser scanners.
New digital surveying technology doesn’t just help with the design. When managing a large project on-site, it is very hard to see what is going on to track progress and to get a “helicopter view” of the project. Photographs from drones, can be processed using photogrammetry techniques and combined with laser scans to produce a “digital twin” or 3D model of a site.
5D Building Information Modelling
5D Building Information Modelling
Building Information Modelling (BIM) is a standardised process for creating and managing information on a construction project across the project lifecycle.
One of the key outputs of this process is the Building Information Model; the digital description of every aspect of the built asset. This model draws on information assembled collaboratively and updated at key stages of a project. Creating a digital Building Information Model enables a better, more joined-up design with fewer clashes and errors that leads to a reduction in the time and cost of construction.
BIM as a concept and a process has been around for a decade or more. For complex construction, the benefits are well proven and as result, lots of large clients (including the UK government) mandate that a BIM process is followed and an international standard (ISO19650) is used to help organisations work together consistently.
We find that in practice BIM does not necessarily make the design process cheaper, rather it allows a better-quality design to be produced that saves 5%-15% in the construction costs on-site due to better information, fewer clashes and problems.
Like most technology enabled approached, BIM can be done badly (often to tick a compliance box) or well (to really help people work better).
All the companies sponsoring this publication use BIM to deliver projects. Some of them have even got to the stage where all their projects use a BIM process because the benefits to clients and the companyare so clear and compelling.
Once companies have mastered BIM in three dimensions, then information on other dimensions can be included and brought into the process.
The fourth dimension is time, so 4D starts to link the design and plans together, so that the construction programme can be simulated. We find that, when done well, this can spot and solve all sorts of problems at the design stage that otherwise would only appear when you are in construction.
This makes the construction cheaper, less risky, quicker and can be used to avoid disruption by spotting, in advance, times where construction will block access, cut power or cause problems to existing operations and neighbours.
5D brings cost fully into the BIM process. In the traditional design process the clients, designers and engineers don’t really understand the cost implications of the decisions they are making. The traditional process of counting and pricing all the materials and labour needed for the construction is slow, manual, uses poor data, is often wrong and comes too late. Increasingly, companies are starting to harness data to improve the quality of estimates and digital technology to automate the costing process. This brings an ability to check the cost of design choices as you go – to really design to a budget and make the inevitable trade-off decisions of time, cost, quality and user requirements as you go.
This 5D process is in the early stages of adoption, as very few companies in the construction industry systematically capture cost data, and even fewer are willing to share that valuable information.
Nevertheless, the experience of our sponsor companies is that there are big advantages to speeding up the costing process and using the best available data to make better informed decisions as you go.
The technology required for 5D BIM is available. Lots of tools for designing in 3 or more dimensions, capturing data, sharing it (through cloud based Common Data Environments) and digital toolsets for planning, simulation and cost estimating have been available for years.
To make it work well though, from the start to finish of a project, requires substantial changes to the ways of working, not just within a discipline, but across the whole supply-chain and project team.
We call this 5D Way of Working (5D WoW). The real challenge of using digital well in your project is not just about picking suppliers that have digital tools, it is also about finding partners that know how to work well in a digital environment and are happy to collaborate and share data with others on your project to get the best result.
Building Information Modelling (BIM) is a standardised process for creating and managing information on a construction project across the project lifecycle.
One of the key outputs of this process is the Building Information Model; the digital description of every aspect of the built asset. This model draws on information assembled collaboratively and updated at key stages of a project. Creating a digital Building Information Model enables a better, more joined-up design with fewer clashes and errors that leads to a reduction in the time and cost of construction.
BIM as a concept and a process has been around for a decade or more. For complex construction, the benefits are well proven and as result, lots of large clients (including the UK government) mandate that a BIM process is followed and an international standard (ISO19650) is used to help organisations work together consistently.
We find that in practice BIM does not necessarily make the design process cheaper, rather it allows a better-quality design to be produced that saves 5%-15% in the construction costs on-site due to better information, fewer clashes and problems.
Like most technology enabled approached, BIM can be done badly (often to tick a compliance box) or well (to really help people work better).
All the companies sponsoring this publication use BIM to deliver projects. Some of them have even got to the stage where all their projects use a BIM process because the benefits to clients and the companyare so clear and compelling.
Once companies have mastered BIM in three dimensions, then information on other dimensions can be included and brought into the process.
The fourth dimension is time, so 4D starts to link the design and plans together, so that the construction programme can be simulated. We find that, when done well, this can spot and solve all sorts of problems at the design stage that otherwise would only appear when you are in construction.
This makes the construction cheaper, less risky, quicker and can be used to avoid disruption by spotting, in advance, times where construction will block access, cut power or cause problems to existing operations and neighbours.
5D brings cost fully into the BIM process. In the traditional design process the clients, designers and engineers don’t really understand the cost implications of the decisions they are making. The traditional process of counting and pricing all the materials and labour needed for the construction is slow, manual, uses poor data, is often wrong and comes too late. Increasingly, companies are starting to harness data to improve the quality of estimates and digital technology to automate the costing process. This brings an ability to check the cost of design choices as you go – to really design to a budget and make the inevitable trade-off decisions of time, cost, quality and user requirements as you go.
This 5D process is in the early stages of adoption, as very few companies in the construction industry systematically capture cost data, and even fewer are willing to share that valuable information.
Nevertheless, the experience of our sponsor companies is that there are big advantages to speeding up the costing process and using the best available data to make better informed decisions as you go.
The technology required for 5D BIM is available. Lots of tools for designing in 3 or more dimensions, capturing data, sharing it (through cloud based Common Data Environments) and digital toolsets for planning, simulation and cost estimating have been available for years.
To make it work well though, from the start to finish of a project, requires substantial changes to the ways of working, not just within a discipline, but across the whole supply-chain and project team.
We call this 5D Way of Working (5D WoW). The real challenge of using digital well in your project is not just about picking suppliers that have digital tools, it is also about finding partners that know how to work well in a digital environment and are happy to collaborate and share data with others on your project to get the best result.
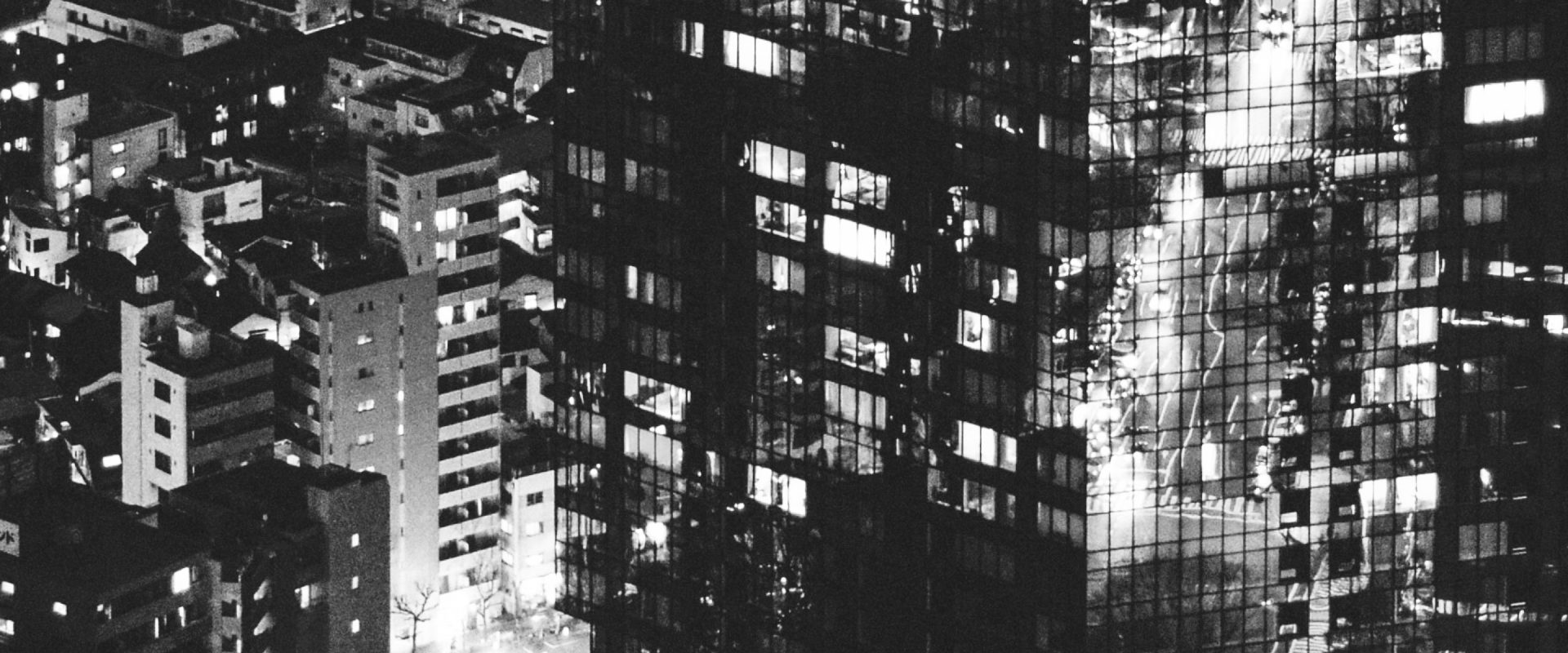
Digital Collaboration and Mobility
Digital Collaboration and Mobility
The ability to share information, documents and designs with other people wherever they may be is an obvious use of digital technology. The design of a complex building or infrastructure requires lots of different people to be involved. Making sure that information is available to the right people when they need it, that questions can be asked, and issues resolved easily (in a digital workflow) and that things aren’t forgotten about is standard fare in a digitally enabled process.
In contrast, the traditional process relies on people producing documents separately, circulating documents for review or having review meetings, and the movement of lots of paper or emails with plenty of room for error or the wrong version to be used. This can be slow, error prone and expensive.
A digital approach to work and collaboration uses cloud-based systems which allow people to have access from different companies and locations, to the same shared information. That information is very controlled and logged. Access can be from desktop computers, laptops, tablets and mobile phones. So, someone on a construction site can look at the latest drawings, zoom in on a 3D model of the design, and send questions or changes to the engineer for quick answers.
By contrast the traditional approach involves paper drawing in 2D, possibly not up to date, and questions by letter, email and phone call that may not get answered in time or even at all; with lots of administrators and project managers trying to keep all the information moving.
Modern cloud-based Common Data Environments for design and construction have been around for more than a decade. There are many different options available each with their own advantages.
The more complex a project is, the more varied the locations of the project staff, and the greater the value of a Common Data Environment (CDE). The companies sponsoring this publication, all use CDEs and recommend them to their clients.
One thing to watch out for is who controls the CDE and, most importantly, the data in it (some of which you will want to keep for operations, maintenance, demolition and future upgrades). We tend to advise clients to procure the CDE themselves (and then get one of the suppliers to manage it), to keep control of the data. At the very least clients need to make sure that contractually, and in reality, they keep control of the data that is essential to their project.
The ability to share information, documents and designs with other people wherever they may be is an obvious use of digital technology. The design of a complex building or infrastructure requires lots of different people to be involved. Making sure that information is available to the right people when they need it, that questions can be asked, and issues resolved easily (in a digital workflow) and that things aren’t forgotten about is standard fare in a digitally enabled process.
In contrast, the traditional process relies on people producing documents separately, circulating documents for review or having review meetings, and the movement of lots of paper or emails with plenty of room for error or the wrong version to be used. This can be slow, error prone and expensive.
A digital approach to work and collaboration uses cloud-based systems which allow people to have access from different companies and locations, to the same shared information. That information is very controlled and logged. Access can be from desktop computers, laptops, tablets and mobile phones. So, someone on a construction site can look at the latest drawings, zoom in on a 3D model of the design, and send questions or changes to the engineer for quick answers.
By contrast the traditional approach involves paper drawing in 2D, possibly not up to date, and questions by letter, email and phone call that may not get answered in time or even at all; with lots of administrators and project managers trying to keep all the information moving.
Modern cloud-based Common Data Environments for design and construction have been around for more than a decade. There are many different options available each with their own advantages.
The more complex a project is, the more varied the locations of the project staff, and the greater the value of a Common Data Environment (CDE). The companies sponsoring this publication, all use CDEs and recommend them to their clients.
One thing to watch out for is who controls the CDE and, most importantly, the data in it (some of which you will want to keep for operations, maintenance, demolition and future upgrades). We tend to advise clients to procure the CDE themselves (and then get one of the suppliers to manage it), to keep control of the data. At the very least clients need to make sure that contractually, and in reality, they keep control of the data that is essential to their project.
The Internet of Things and Smart Cities/ Smart Buildings/ Smart Transport
The Internet of Things and Smart Cities/ Smart Buildings/ Smart Transport
The Internet of Things (IoT) is a set of technologies that provide low-cost, connected sensors that can measure things and report back data to the cloud. IoT has all sorts of applications in making buildings, infrastructure, transport and even whole cities “smart”. We think that any new development of scale should be thinking hard about the data that could be useful and building smart into the design.
For example:
- Smart street lighting that adjusts the lighting based on traffic, weather etc. can save up to 40% of the energy. It can alert maintainers to problems, reducing maintenance and is also a great platform for attaching sensors for things like air-quality that you want to measure.
- Smart motorways are long established in some countries. There sensors are used to monitor the roads, and to adjust signs to smooth traffic flow, and often to enable the “hard shoulder” to be used as an additional lane, unless needed for a breakdown or accident.
- Smart buildings use sensors, and integration with the Building Management Systems to improve the monitoring and control of a building. Improving utilisation of space, improving air quality, reducing energy usage, and reducing building risk are all possible.
However, we also urge some caution; the core IoT sensor technology works very well, but being able to process, understand get real value from the data is hard and a lot of solutions don’t seem to quite get the benefit.
An approach we typically recommend to clients is to think about the questions you want answers to, from the smart data and work back from that to gather the right data. If you don’t know or can’t know yet the questions you want answers from, then including sensors and data storage in the base design is relatively low-cost bit of future proofing.
For example, Pell Frischmann manages the facilities management services for numerous schools. This includes maintenance and energy. They have installed technology to pull data from the BMS and have added low-cost IoT sensors.
As a result, they now have 100’s of data streams showing the temperature and usage in each room, the actions of each pump in the heating system, the water temperature going in and out of the boiler etc.
The most difficult part was not the technology, but analysing the data, and producing simple graphs that the building managers can use. As they have solved the analytics challenge, they now have found actions to improve the efficiency of the heating system, reduce times when the heating was on, and reduce maintenance.
The Internet of Things (IoT) is a set of technologies that provide low-cost, connected sensors that can measure things and report back data to the cloud. IoT has all sorts of applications in making buildings, infrastructure, transport and even whole cities “smart”. We think that any new development of scale should be thinking hard about the data that could be useful and building smart into the design.
For example:
- Smart street lighting that adjusts the lighting based on traffic, weather etc. can save up to 40% of the energy. It can alert maintainers to problems, reducing maintenance and is also a great platform for attaching sensors for things like air-quality that you want to measure.
- Smart motorways are long established in some countries. There sensors are used to monitor the roads, and to adjust signs to smooth traffic flow, and often to enable the “hard shoulder” to be used as an additional lane, unless needed for a breakdown or accident.
- Smart buildings use sensors, and integration with the Building Management Systems to improve the monitoring and control of a building. Improving utilisation of space, improving air quality, reducing energy usage, and reducing building risk are all possible.
However, we also urge some caution; the core IoT sensor technology works very well, but being able to process, understand get real value from the data is hard and a lot of solutions don’t seem to quite get the benefit.
An approach we typically recommend to clients is to think about the questions you want answers to, from the smart data and work back from that to gather the right data. If you don’t know or can’t know yet the questions you want answers from, then including sensors and data storage in the base design is relatively low-cost bit of future proofing.
For example, Pell Frischmann manages the facilities management services for numerous schools. This includes maintenance and energy. They have installed technology to pull data from the BMS and have added low-cost IoT sensors.
As a result, they now have 100’s of data streams showing the temperature and usage in each room, the actions of each pump in the heating system, the water temperature going in and out of the boiler etc.
The most difficult part was not the technology, but analysing the data, and producing simple graphs that the building managers can use. As they have solved the analytics challenge, they now have found actions to improve the efficiency of the heating system, reduce times when the heating was on, and reduce maintenance.
Our Recommendation
You don’t need to be an expert in the technology, but you do need to have enough of an understanding of what the technology can do for you and your colleagues who will use the built asset.
A well informed client that knows what they really want and need, enables the supply-chain to use technology better to deliver in the right way for you. This guide is intended to be a help in understanding a bit about what the technology can do.
We do recommend talking widely to your colleagues to understand the business benefits, risks and issues and relative importance of time and cost, but also operational risks, customer experience and environmental sustainability.
If you would like to know more please click on one of our sponsors: