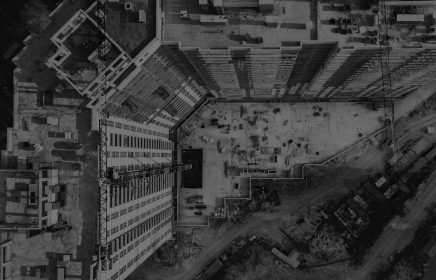
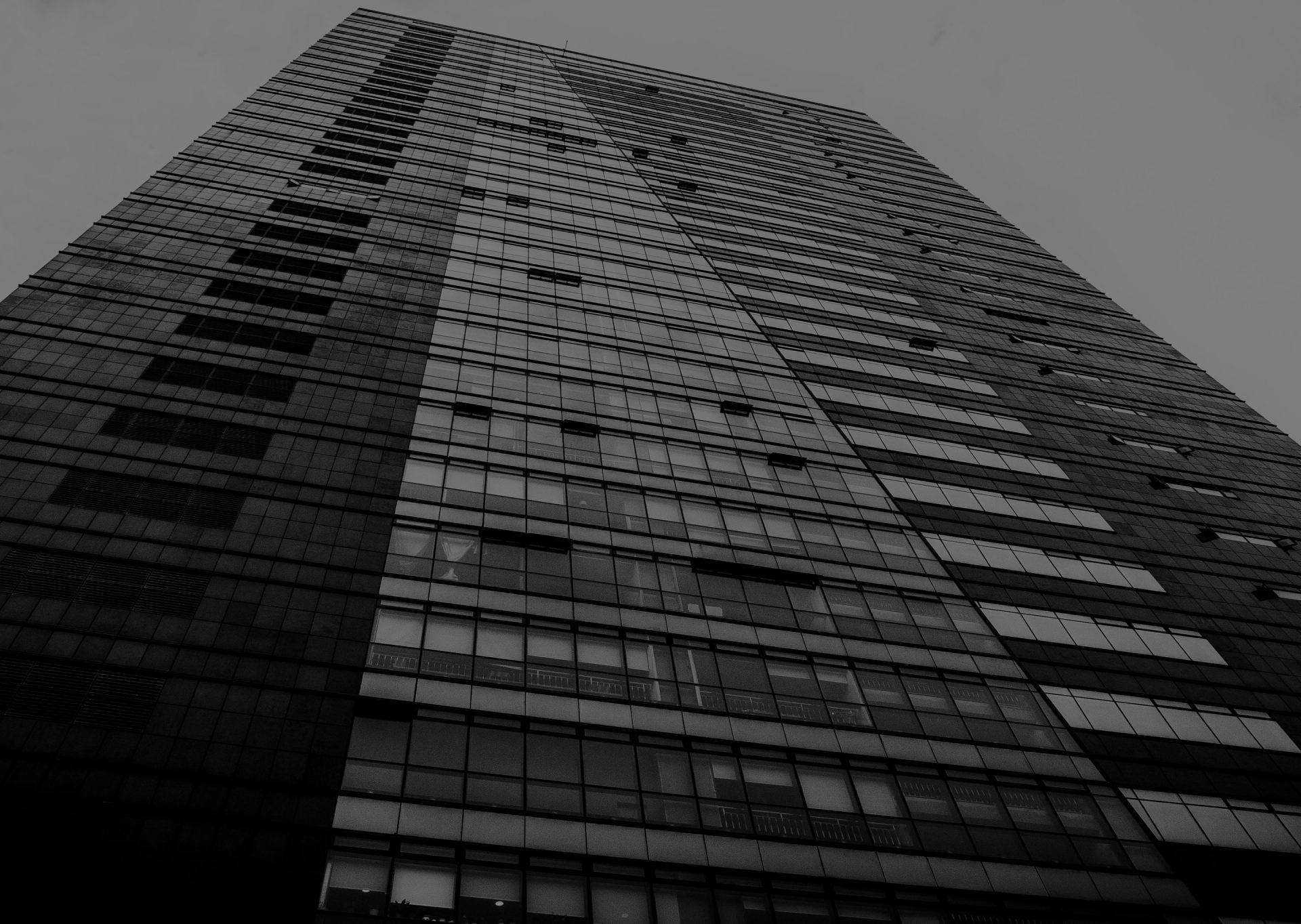
Getting the Most Value from your Asset
The promise of BIM.
Part of the promise of BIM and digital is in using data and digital technology more intelligently, to reduce the cost of running and maintaining buildings. So far, this is an area in which practical project reality has largely failed… Read More
The promise of BIM.
Part of the promise of BIM and digital is in using data and digital technology more intelligently, to reduce the cost of running and maintaining buildings. So far, this is an area in which practical project reality has largely failed to deliver on the promise. There are two major elements to this, which are worth thinking about.
Part of the promise of BIM and digital is in using data and digital technology more intelligently, to reduce the cost of running and maintaining buildings. So far, this is an area in which practical project reality has largely failed to deliver on the promise. There are two major elements to this, which are worth thinking about.
The two major elements to BIM:
1
Passing useful data from Design and Construction, to Operations and Maintenance
The design process creates a lot of data about the building, it’s geometry and systems which should be useful for maintaining and running the building. This particularly applies to complex, maintenance heavy built assets, such as railways, hospitals and factories, but should apply also to office buildings or blocks of shopping centres. The challenges in making that work are multiple and therefore, caution is sensible in investment.
Challenges include:
- Operators and maintainers are often not involved in the design or asked about what data they need
- Large quantities of the data from design is not useful after construction and it takes some effort to collect and prepare the data, and translate it to the asset-management/facilities management systems
- Operations and maintenance are often not set-up to use digital data and to keep digital records up to date. If data is not maintained, then eventually it becomes useless.
For most clients, the key is to work out your project which data is really useful for operations and maintenance, and make sure that will be delivered in the right way. Usually the most useful information is data on the Mechanical, Electrical and Plumbing systems, that have the most maintenance.
At least providing the specifications, manuals and part numbers for those systems (usually in a Construction Operations Building Information Exchange (COBie) format) will be useful in the future.
2
Building the right smart technology into the design
Putting sensors into modern infrastructure and buildings is generally a sensible thing to do. The Smart Building/Infrastructure/City concept is a good one in general, but hard to get right in practice.
The challenges here are:
The technology is evolving fast, but the buildings or infrastructure will last for decades or even centuries. The best answer is to use open standards and data architecture, and allow flexibility in the design, so that additional technology and uses can be added.
Getting useful insight that will actually be used to improve things. For example, Smart Motorways are well established (in the UK) and work well increasing road capacity by using the hard shoulder intelligently, monitoring flows in a control centre and using digital signs to affect driver’s behaviour. There is an established programme, the benefits are proven, and it works. 4Way are heavily involved in the UK programme and have commissioned 70% of the motorways delivered.
When we look at Smart Buildings however things are less clear; energy saving, environmental impact, a comfortable environment for users, improving building utilisation and reducing the risk from fire and flood are all cases for smart buildings.
In the experience of the organisations sponsoring this publication, the smart building technology works well but turning the wealth of data into action and value is not so easy. It is one thing generating hundreds of data streams and graphs from a building, it is another step to create simple and easy-to-use analytics that will tell the building operators how to save energy or adjust the building parameters dynamically.
Our recommendation is to spend time in the early stages of building design working out what information is really needed and being clear how that information should be presented. Involving the people who will operate the building in the design process can really help in working out what would really be useful and building it into the design.
After all, with a building or a piece of infrastructure the construction cost is only part of the long-term life-cycle cost of the facility. Using smart technology to get a better environment, at lower cost, with lower carbon usage and higher space utilisation makes great business sense and has impact for many years to come.
Monitoring and inspection for safer infrastructure.
When an old structure collapses unexpectedly the danger, expense and disruption can be huge. For example, the Genoa, Morandi bridge collapse in 2018 which killed 43 people, left 600 people homeless and has caused enormous disruption. Regular inspection of structures is therefore important. In… Read More
Monitoring and inspection for safer infrastructure.
When an old structure collapses unexpectedly the danger, expense and disruption can be huge. For example, the Genoa, Morandi bridge collapse in 2018 which killed 43 people, left 600 people homeless and has caused enormous disruption. Regular inspection of structures is therefore important.
In most countries, these are highly labour intensive and use manual processes. Dorsch Gruppe inspects road structures for the Abu-Dhabi municipality, and this requires manual checks such as using a sounding hammer as well as electronic tests for corrosion and ultrasonic changes.
Similarly, the railway bridge checks that Pell Frischmann carry out require the closure of the bridge, so that an engineer can inspect it carefully close up.
Digital stress monitoring systems do exist and work well; Pell Frischmann uses them to monitor old railway tunnels in London for problems caused by being underneath a major construction project. This tunnel monitoring even uses Artificial Intelligence, to look for changes and alert engineers. Drones are useful for visual inspection, without having to put up scaffolding. When it comes to health and safety legal requirements for inspection, however, things are rightly slow to change. It will take many years to prove that stress sensors and drones can provide at least as much assurance, as traditional manual inspection.
Until the new techniques are proven, the requirement for physical inspection won’t go away.
The approach we recommend is to start to use the new techniques in parallel. There are great benefits to building up comparable data over time, that will enable much more informed and precise decision making.
The early warnings that such systems can provide, and much more frequent monitoring should over time save lives and reduce costs and disruption for infrastructure owners. Including sensors in the specification for new builds is low cost.
Adding sensors when inspecting structures or using drones as part of the inspection process, does not add much cost but will improve the inspection. Eventually, the legal requirements will catch-up once digital inspection and monitoring is proven.
When an old structure collapses unexpectedly the danger, expense and disruption can be huge. For example, the Genoa, Morandi bridge collapse in 2018 which killed 43 people, left 600 people homeless and has caused enormous disruption. Regular inspection of structures is therefore important.
In most countries, these are highly labour intensive and use manual processes. Dorsch Gruppe inspects road structures for the Abu-Dhabi municipality, and this requires manual checks such as using a sounding hammer as well as electronic tests for corrosion and ultrasonic changes.
Similarly, the railway bridge checks that Pell Frischmann carry out require the closure of the bridge, so that an engineer can inspect it carefully close up.
Digital stress monitoring systems do exist and work well; Pell Frischmann uses them to monitor old railway tunnels in London for problems caused by being underneath a major construction project. This tunnel monitoring even uses Artificial Intelligence, to look for changes and alert engineers. Drones are useful for visual inspection, without having to put up scaffolding. When it comes to health and safety legal requirements for inspection, however, things are rightly slow to change. It will take many years to prove that stress sensors and drones can provide at least as much assurance, as traditional manual inspection.
Until the new techniques are proven, the requirement for physical inspection won’t go away.
The approach we recommend is to start to use the new techniques in parallel. There are great benefits to building up comparable data over time, that will enable much more informed and precise decision making.
The early warnings that such systems can provide, and much more frequent monitoring should over time save lives and reduce costs and disruption for infrastructure owners. Including sensors in the specification for new builds is low cost.
Adding sensors when inspecting structures or using drones as part of the inspection process, does not add much cost but will improve the inspection. Eventually, the legal requirements will catch-up once digital inspection and monitoring is proven.
Our Recommendation
Operations and maintenance people are often not involved in design and construction until handover. Some time spent in early design stages on understanding what information can make the asset easier to manage can make a big difference later on. Use virtual reality to get users to experience a building during the design and even to get maintainers to experience the plant and systems to make sure the design is right.
If you would like to know more please click on one of our sponsors: